Our Clients Receive the DMC Estimating and Project Management Platform V11.0 for Free (A $5,995 value). Email dmc@millworkconsultant.com for information
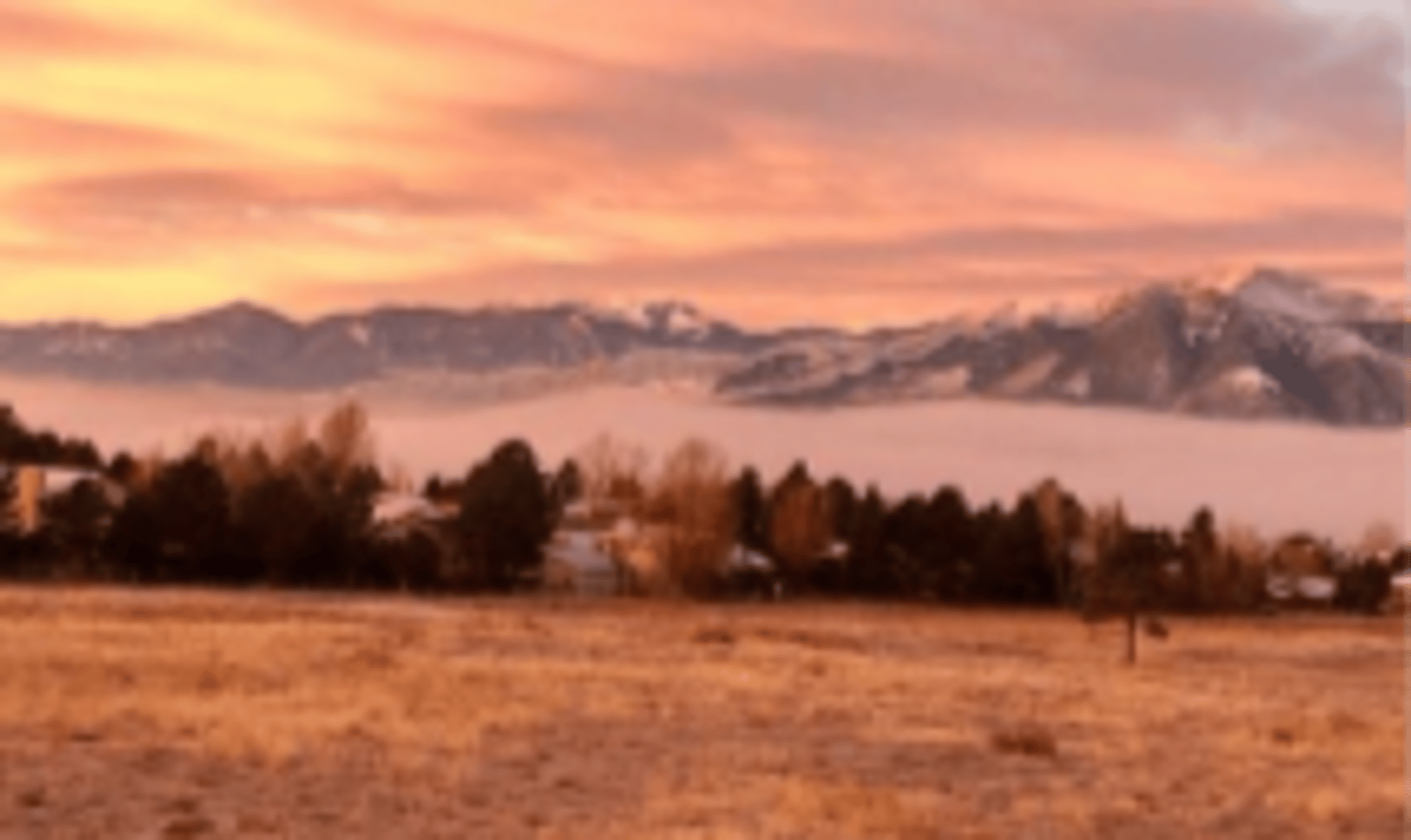
DMC Millwork Consultation
Seminars in Contract Negotiation, Estimating, Project Management, Purchasing, and Total Company Integration.
Total Company Integration Analysis Provided, Efficiency Advising, Sales, Project Management, Candidate Searches & Estimating.
Contact: dmc@millworkconsultant.com
Office: 719-488-2759, Mobile 719-755-8897
BLOGS
Hello DMC clients,
Any projects that are heavy with metal aspects should be contracted as soon as possible, or significant escalation should be accounted for.
More than 2/3 or our aluminum, more than 1/2 brass and copper, and 1/4 of our steel comes from China. Germany makes up a significant exporter of metals to us as well. As you may have heard, things with China aren't doing very well. Germany can't produce metals to a good level anymore because Russia is squeezing their natural gas supply.
Further, regulatory agencies in the US are ramping up their restrictions and expenses for companies that produce and recycle metal raw material, at the worst time.
So expect some extreme volatility in this arena in coming months, especially if China decides to reduce or eliminate these exports to the US. It would be a good idea to inform the GC's, designers and owners of this on all future projects.
Thanks,
MATTHEW D. CREECH, PARTNER
Millwork Consultant in
Sales, Estimating, Efficiency, Production and Project Integration
DMC
millworkconsultant2@gmail.com
C: 719-375-9470
www.millworkconsultant.com
Why Small-Sized Channel Forming Can Be A Challenge
Customers are often baffled by an over-the-phone explanation of why certain sized channels cannot be press brake formed. Although press braking appears to be a simple concept, precision accuracy can be quite difficult.
If the channel has vertical legs that are too long when compared to the base, the leg formed first will crash into the forming dies before the second bend bottoms out at 90 degrees. When that happens the metal will crash into the brake or forming dies and the legs or base (or both) will be stretched and contorted, which basically ruins the channel.
Sometimes these constraints can be overcome. Here are some suggestions when forming small-sized or deep-leg channels:
Custom “dog leg” or “gooseneck” or “swan neck” dies (shown in Figure 2) can often be used or special ordered that allow for tighter formed channels.
Most metal fabricators will have a few sets of standard gooseneck dies for basic channel forming but often times custom sets of metal forming dies will have to be ordered to form and fabricate the parts needed. These types of dies are expensive, costing several hundred dollars per foot so smaller-sized jobs, particularly non-repeat jobs, are often not quoted because of the excessive cost of purchasing a custom die set.
Some fabricators will suggest “back-bending” the metal channel, which is also hard to explain verbally but can be attempted.
Back bending works by creating a “W” shape in the formed part and then hitting the channel again with a flattening die to smash the middle section out of the “W” .
Back bending... keeps the leg of the die from smashing into the crash-point as shown in the illustration. This works well when there may be only a few parts to bend and the fabricator and customer decide, jointly, that it makes sense.
There are a few drawbacks to this method.
One, the metal part will have a line down the middle of the channel where the metal was flattened, which may or may not be important depending on how the part is used.
Two, this is not a very efficient way of forming parts because it takes several press brake setups and multiple handling of parts compared to basically one set up if the part was formed with the gooseneck dies.
All of this is simply to say that forming small or deep channels in sheet metal, as we originally pointed out, is not as easy and obvious as one might think.
Hopefully, this will help you as you work with your local metal fabricator.
Future metal fabrication and press brake forming topics that relate to this will include forming fractures (when metal actually fractures or breaks as it is formed), minimum forming dimensions (what is too small to form) and forming to inside or outside dimensions.
Source: www.allmetalsfab.com/why-small-sized-channel-forming-can-be-a-challenge/
10-5-18
Why Cheap Design Is Costly
By Matthew Creech
This message is for owners and designers, although I know that pretty much the only folks who read this will be subcontractors. There is a new trend that is picking up steam in the architecture and design industry. I call them "econodrawings". Maybe the owner paid or will pay the designers a hefty sum, but the drawings look like something a bored high school student would scribble during algebra class on how to build a bike ramp. These drawings often comically ( or frustratingly) showcase esoteric rectangles left to interpret, sections and elevations that seem to be for different items, finish schedules that conflict with finish plans, or project manuals (specs) that don't match ANYTHING. If you detect frustration in my literary voice, you're catching what I'm throwing.
Econodrawings betray the GC assuring us that "oh no, we'll be awarding off of these documents" statement. They tell the subcontractor that "well, if I do this I will have X number of addendums, bulletins, etc". Econodrawings make us want to raise the price, just because. Econodrawings almost always have us scratching our heads exclaiming things like: "wait, that material doesn't bend like that", or "that company doesn't even make that material" to "how am I going to get this 50 foot long contraption in a powdercoating oven?"
Just recently, our company was representing a client bidding on a high end office fitout in the DC area. The designer was one of the biggest and most well known on the East coast. I saw an elevation that looked oddly familiar to me, and there were 4 sections with references that didn't even exist in the drawing set. Then it hit me. I realized that the designer just copied and pasted from another project, but forgot to change the section tags. Can you believe, the designer will probably get paid 5-10% of the project price ($4 million dollars, by the way). If you or I were that (insert derogatory adjective), we would be out of business, sued, laughed at, ridiculed, and rightfully so.
Now, I am not just shooting off here for the sake of protest. There is a some good advice here you can relay to owners. If an owner or owner's rep is reading this, relay this to yourself. You see these econodrawings are costing owners a lot. Maybe people get enamored with the big names of the design firms they hired, but I have seen countless times where the small time designers are far superior and save the owner much more money. Let's examine why.
Poor drawings force more and more addendums to be released. Many subcontractors do not have the resources to bid projects over and over again with the hope that someday a contract will fall from heaven. As subcontractors pull out, the general contractors have less and less players to choose from. As the process continues, I have seen contractors bluff where they say they still have subs in hunt, but in reality they only have one or two left. Subs are savvy to this (I am trained to know when we are the only show in town) and realize they can bump their prices up. I think that designers convince owners that going through this "budgeting" process will help hold down costs, when in reality it just alienates subs and leaves only the most expensive dogs in the race.
Poor drawings force subs to interpret on the high end to protect themselves. For example, let's say that the drawings show architectural metal angle trims scaled to show a 1/4" thickness, and are not clarified. Let's say that the designer specifies oil rubbed bronze finish. We would price this at about $50 - $65 per linear foot. Then, we find out later that intent was 1/8" anodized aluminum finished to look like bronze (about $7-$10 per linear foot). The costs difference could be tens, even hundreds of thousands of dollars (this actually happened). Realizing the error, the designer at the last minute makes corrections, but the subs (due to the pain of it all) reduce price down to $20 per linear foot. Because the owner doesn't know better, he or she thinks that the price was reduced but doesn't realize it could have been a lot cheaper in the first place.
Good drawings show every little necessary detail, and a good designer shows no ignorance in materials, installation, and feasibility. A good example is hospitals. I'm not sure why this is, but hospitals tend to have higher quality drawings than, lets say, apartments. When a subcontractor looks at drawings that are well done, he will sharpen his pencil and price things as tightly as possible, because he knows no one else will get scared off by the drawings. Also, he knows that multiple addendums are less likely, and will probably hang on through the bid process longer. This will give the owner and general contractor more leverage to negotiate with the subs.
Good drawings leave nothing to chance. Anything left to interpretation by a subcontractor will mean an unnecessary increase in price. Even after clarification almost no subs will go down to a price as was hoped for or intended.
My last bit of advice to owners: I would ask for designers to show drawings for at least 5 different projects they have completed before hiring. Then pay a subcontractor a small fee to look things over, and get some advice. Their input could save tens, even hundreds of thousands of dollars!

© 2024. All rights reserved.